Over forty years ago, my late father brought a Mamod steam engine into the home, screwed it down onto a strip of chipboard, and made it run. I can not remember now if it was a toy for me or a toy for him. Eventually, like childish things, it was put away, in a shoe box, oily and forgotten, the line shaft axle bent, the drive bands and safety valve lost. Not quite forgotten though: I wanted to restore it and, in the time of COVID-19, I did.
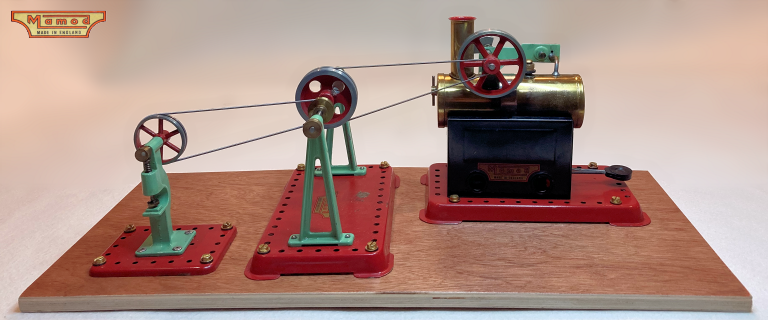
Mamod Minor 2
The engine is a Mamod Minor 2 (MM2), with a boiler an inch longer than its sister model MM1. It has an overflow plug at the front of the boiler, which dates it between 1975 (when plugs were introduced) and 1978 (when the overflow plug was replaced by a sight glass). It also has a solid fuel burner, which dates it from 1977. The MM1 and MM2 were discontinued in 1979. I must have been eleven, maybe twelve, when it last ran.
Together with the engine, I had a line shaft and a model power press.
Marlin (Engineers) Limited’s marketing of Mamod emphasised its interoperability with Meccano. The Mamod bases were drilled with ‘Meccano’ holes, spaced at 0.5 inch and with diameters wide enough to take British Standard Wire Gauge (SWG) 8 axles (0.160 inch, 4.064 mm, diameter); imperial measures from another age. The line shaft axle was a ‘Meccano’ axle.
Spares and consumables
Mamodonline furnished a replacement safety value (0.25 inch British Standard Fine (BSF) thread), 12 inch unjoined drive bands, lubrication oil and solid fuel tablets.
Mounting
A scrap piece of 12 mm marine grade plywood – sawed, sanded and satin varnished – provided a base. The varnish was sufficient to protect the wood from the spray of lubrication oil and overflowing water.
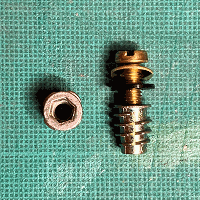
I wanted to be able to remove the attached engine easily, so I used M4 machine screws anchored in flanged threaded inserts for wood. I used brass screws (with slotted cheese heads) and washers but also a black nylon 66 washer between the metal washer and the plate to protect the plate from scratches. Late in the day, I wondered if the nylon washer would be affected as the engine plate became hot. However, nylon 66 can handle temperatures well in excess of the boiling point of water for short periods.
The threaded inserts required 5.5 mm to 6 mm holes. I used a 6 mm drill bit for wood, and a drill guide to ensure the inserts were set vertically.
Steaming
The MM2 is an oscillating cylinder steam engine. Once the stream pressure has built up, the fly wheel needs an initial push in the direction that the engine is to run. A hole in the rocking cylinder aligns alternately with two holes in the block. One hole is the steam port, allowing steam from the boiler to enter the cylinder and force the piston out. The other is the exhaust port, allowing the piston to return as the momentum of the fly wheel carries it round and pushes the piston back into the cylinder.
The boiler is about 1¾ inches (44 mm) in diameter, with a water level plug hole centred about 1¼ inches (32 mm) from its base, and just over 4½ inches in length (about 117 mm). A full boiler therefore holds about 130 ml of water. Hot water reduces the amount of fuel needed to generate steam.
Two 5 g tablets of solid fuel (methenamine, with an energy density of 30 MJ/kg) are sufficient for a single run. Water has a specific heat capacity of about 4.2 kJ/kg/°C and a specific latent heat of vaporisation of about 2,260 kJ/kg. Heating and boiling 130 g of already hot water will require about 330 kJ, the energy supplied by about 11 g of fuel. In practice, the engine runs out of steam, if not literally, when the tablets burn low and there is still a little water in the boiler.
Background music: ‘Confidence’ by Chris Burrink, bundled with Microsoft’s Photos app (Video editor) as music track ‘Together’.